シチズンが
民間月面探査プログラム
「HAKUTO-R」に挑む
宇宙クオリティーを追求する
情熱と技術
ispace /シチズン時計/シチズン時計マニュファクチャリング
HAKUTO-Rコラボレーションモデル
第5弾特設サイト
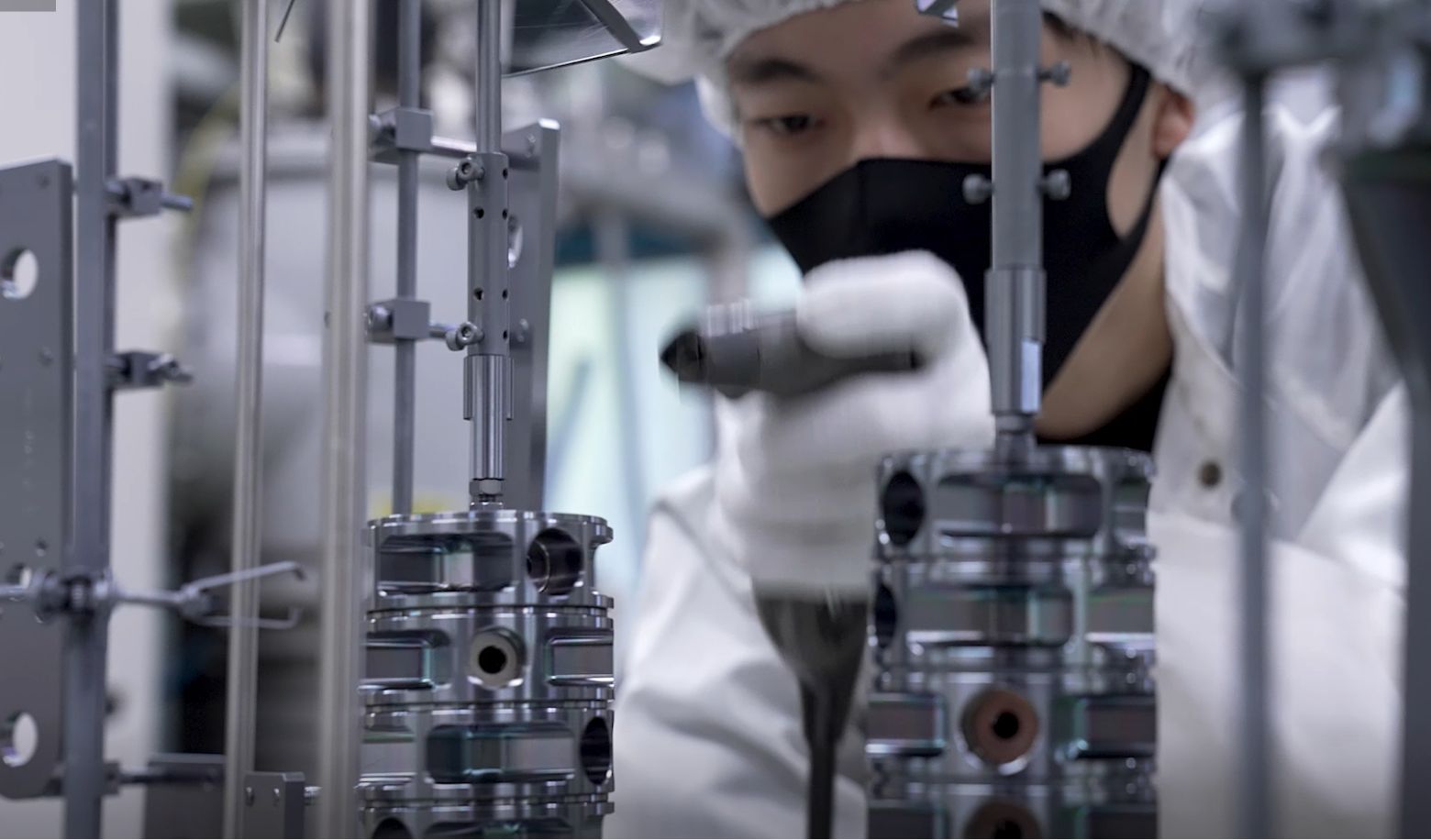
宇宙と時計に、新しい軌跡を。
シチズン時計株式会社は、100周年を迎えた今もなお、常に時計の可能性を考え、開発を続けています。
今回のHAKUTO-Rプログラムへの支援もそのひとつです。その舞台裏には困難を乗り越えるための大きな努力が存在しました。
日々、シチズンを支える技術者たちは何を考え、何を目指しているのでしょうか。
プロジェクトの内側をお届けいたします。
シチズンは民間月面探査プログラム「HAKUTO-R」においてコーポレートパートナーという立場で、2019年からプログラムを支援しており、ランダー(月着陸船)には「スーパーチタニウム™」というシチズンの技術が活かされています。
軽く強く錆びにくいチタニウムに特別な加工を施してあり、こすれたりぶつかったりしてもキズつくことがほとんどないため、ランダーの着陸脚パーツ部分に採用されました。
シチズンのスーパーチタニウム™を
宇宙クオリティに
民間月面探査プログラム「HAKUTO-R」とシチズンの巡り合い
経緯は、月着陸船に使用される部品には、軽量性、摺動性、耐摩耗性などのニーズがあることを知ったことです。そこで、シチズン時計は自社のスーパーチタニウム™(チタニウム加工+表面処理)の技術を宇宙産業に提供し、スーパーチタニウム™を宇宙クオリティにすることを考えました。
これが、民間月面探査プログラム「HAKUTO-R」とシチズンの巡り合いです。
また、今回デュラテクトシリーズの中からダイヤモンドライクカーボン(以下、DLC)が選ばれた理由は宇宙産業でDLCが採用されている実績があること、実際にispaceの技術担当者の方が他社時計とシチズンのDLC処理の時計を両方使用されており、シチズンのDLCはキズがついていないと実感されていたことです。これらのことが採用された大きな契機となりました。
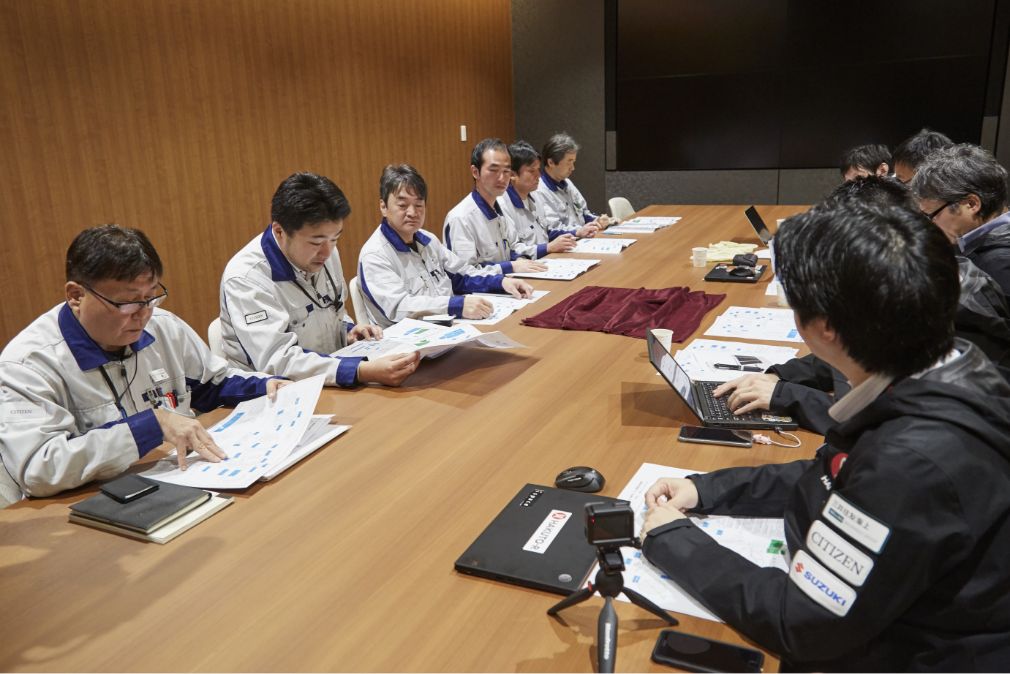
シチズン時計表面処理部門の取り組み
月面探査プログラムについて当初あまり知らず驚いたメンバーも多かったのですが、ispaceの皆さまから直接お話を聞き、非常にチャレンジングでやりがいのある仕事だと実感したシチズンメンバー。
シチズンの表面処理技術も言い換えれば真空技術の応用でもあり、宇宙との親和性は実は非常に高いので、表面処理部門としてこのプログラムに参画することはシチズンにとっても非常に価値のあるものだと感じました。
しかしながら、表面処理部門の専門知識だけでは到底、対応し切れないことばかりだったため、シチズングループ内の様々な技術者へ声をかけ、助けをもらいながら進めていきました。
宣伝部門からの依頼で新聞広告、雑誌、ネット記事など一部メディアにメンバーが出演することにより、HAKUTO-Rの内容についてもメンバーの中でより理解が深まりました。
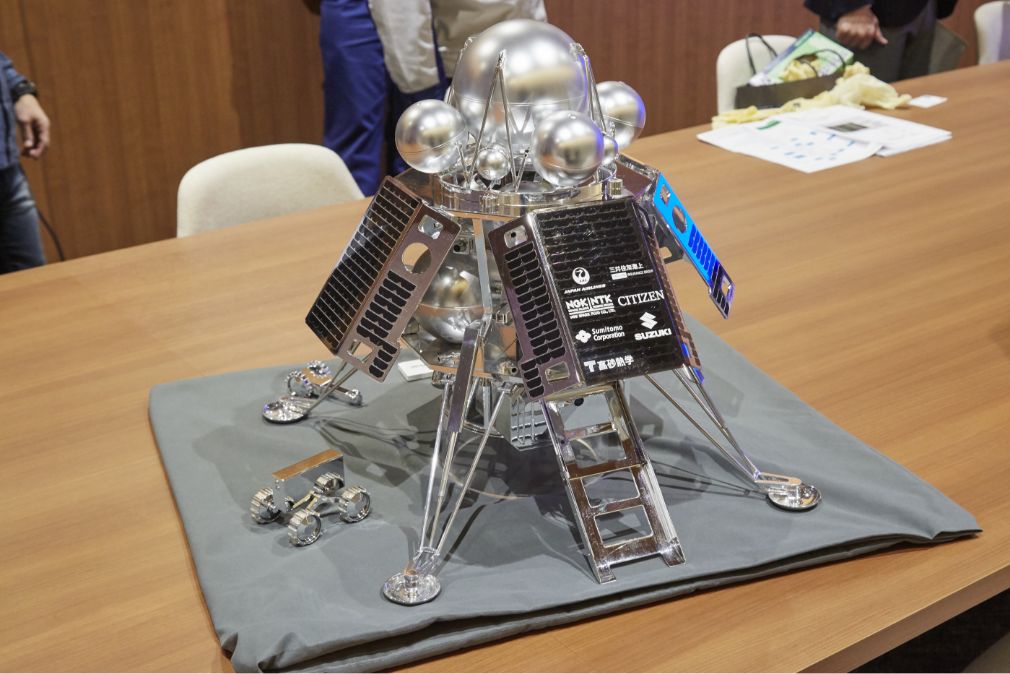
材料調達は、「指定材種を最適寸法形状で短納期で納めること」がカギ
材料はispaceから指定されたチタニウム(チタニウム合金)を使用しました。工業用材料として一般に流通しているものなので、チタニウムを取り扱っている金属卸から調達し、素材として好ましい形状や寸法を機械加工担当のシチズン時計マニュファクチャリングと相談して決めることになったのです。
材料の在庫状況については希望納期に入手可能か否かをよく確認しました。また、材料納品の際には、金属卸に材料証明書を添付してもらい、間違いなくispace指定の材種であることを確認し、完成部品をispaceへ納品した際にも材料証明書を添付しました。
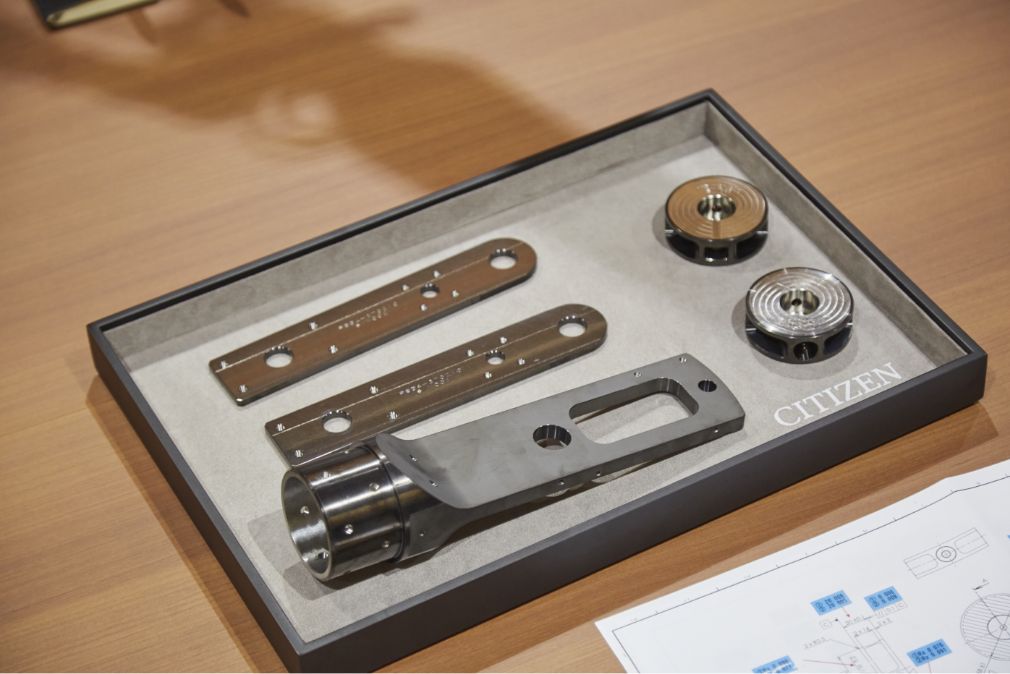
表面処理の難易度の高さ
時計の表面処理では膜の機能(キズつきにくさ)や膜の外観(色、美観)も重要視されますが、HAKUTO-Rのランダー着陸脚部品では特に膜の機能(高い摺動性と耐摩耗性)が重要となります。どのように治具を設計して要求を満たす表面処理を施すか、また部品個数に余分がない一発勝負なのでどのような工程でロスが生じないようにするかが求められました。
また、DLCの成膜前までいかに綺麗な状態でハンドリングするか、DLC成膜装置の内部をいかに綺麗な状態に保つかなど、気を付ける点が沢山ありました。現場のメンバーもワクワクと心配とで複雑な心境だったと思います。試作品ができてispaceに引き渡しをするときは、とても緊張したそうです。
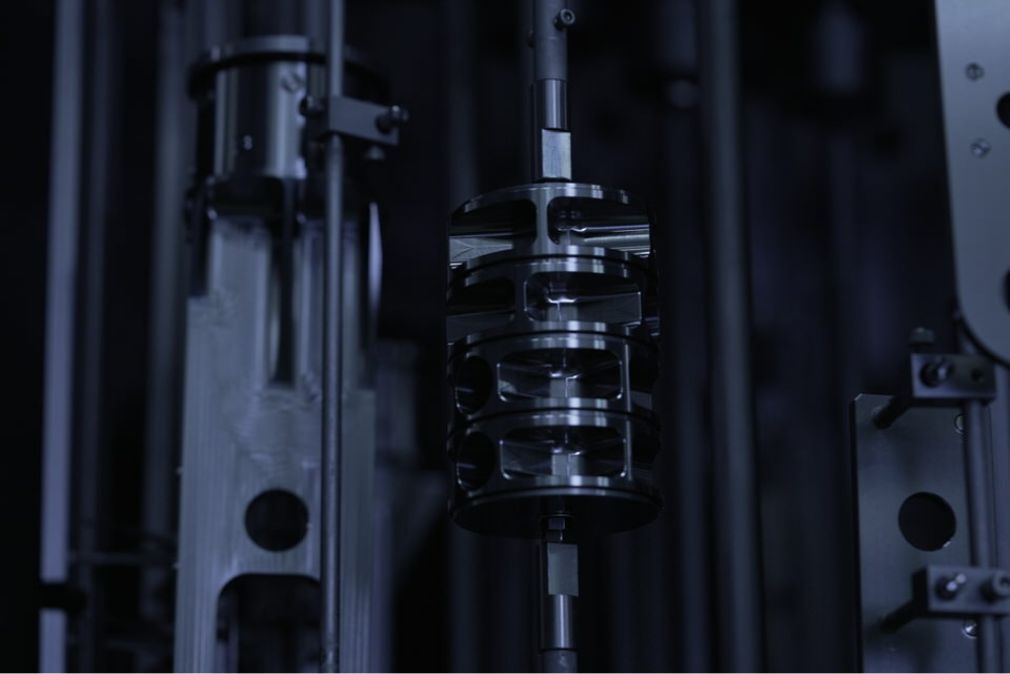
モデル
第5弾特設サイト
シチズン時計マニュファクチャリングの取り組み
部品の機械加工を担当したシチズン時計マニュファクチャリングでは、ランダー脚部のショックアブソーバー内部の部品を製作しました。最初の試作では3軸マシニングセンターと旋盤を使用して作りました。数人で作業を分担して、材料の準備、マシニングセンターで形状を加工して旋盤で表面を仕上げて完成させました。
2度目以降は最新鋭の5軸マシニングセンターで加工することによって、より精度が高い部品を納めることができました。
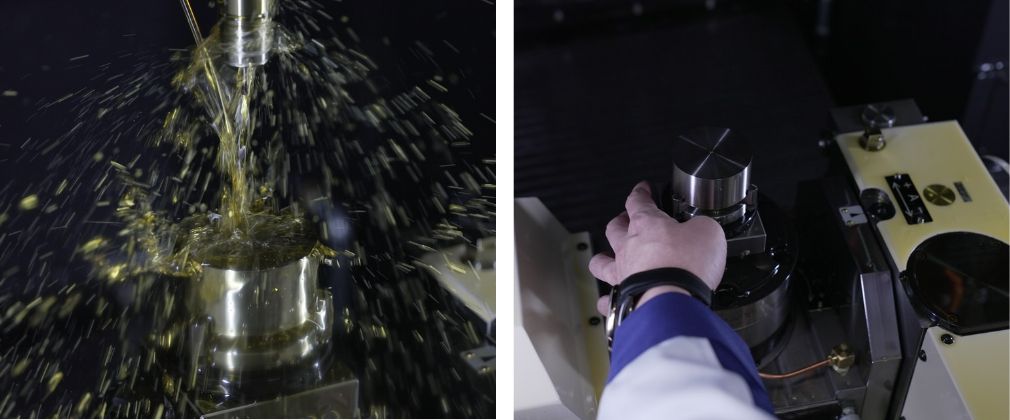
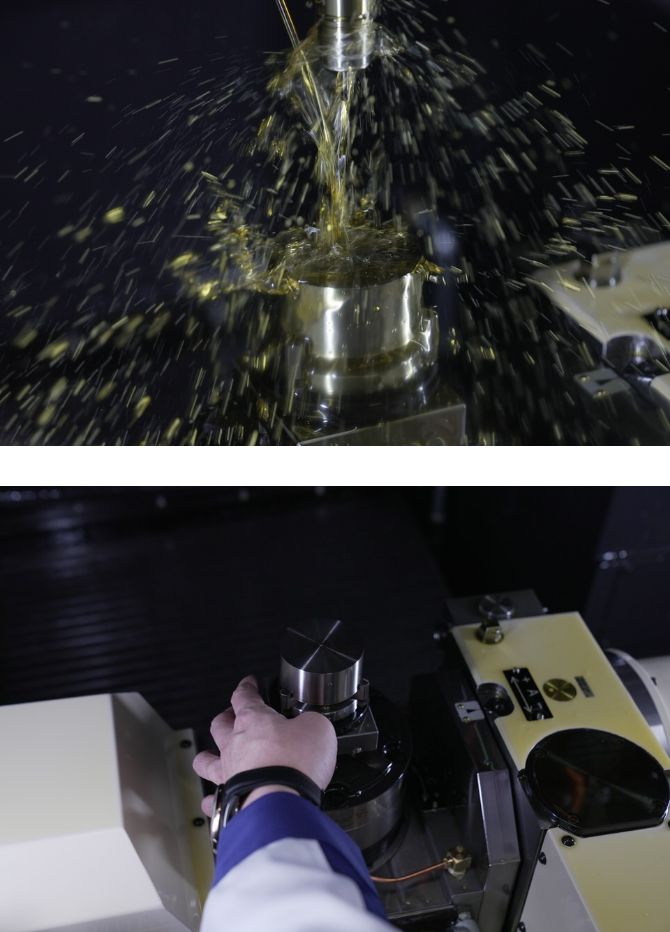
部品自体の加工の難易度は時計製造で培った技術で対応できましたが、月へ行くのかと意識してしまうと、穴や形状の精度をどうしようかなど考えを巡らせてしまいました。はじめは四角い材料から円柱に削ったり、最新鋭の5軸マシニングセンターを使用して加工するときも、全ての部品が検査で合格するまで緊張の連続でした。
検査測定では加工後とDLC成膜後の2回測定を行います。普段あまり行わない3次元的な評価も必要となるため、ispaceの設計者が求めるものは何なのか考えながら工夫して測定を行いました。
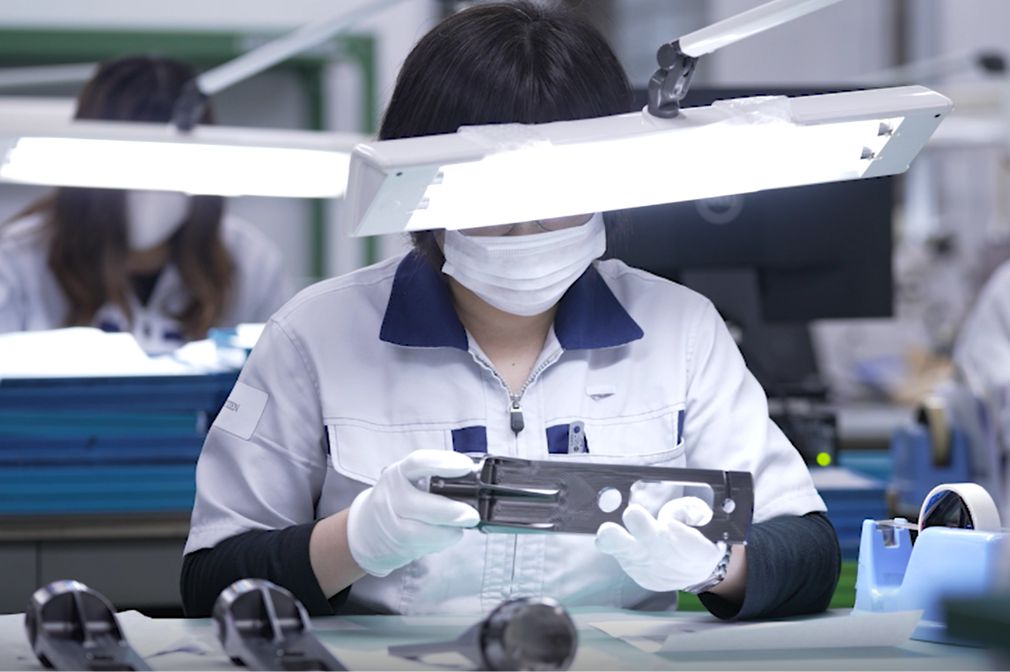
シチズン時計マニュファクチャリングではランダーの着陸脚部品のパーツの加工も行いました。材料はチタニウムで、耐食性・耐熱性・強度も高い材料で航空宇宙業界で活用される金属になります。また、優れた特性を持っていますが加工は難しい金属です。どのように加工するのか意見を出し合い、材料を取り付けるための治工具の設計から行いました。加工は主にマシニングセンターで行い、製作した治具に取り付けて、穴あけ加工や形状加工を行いました。
少しの加工で材料が反ってしまう難切削材であることが、作業上で最も大変でした。反ることにより寸法が出なくなりますし、材料の性質を利用しての加工方法の模索もしなければなりませんでした。どうしたら寸法精度を良く仕上げることができるのか、加工方法はどうしたらいいのか等、課題はたくさんありました。それでもシチズンのチタニウム加工のノウハウを活かして、加工を行いました。
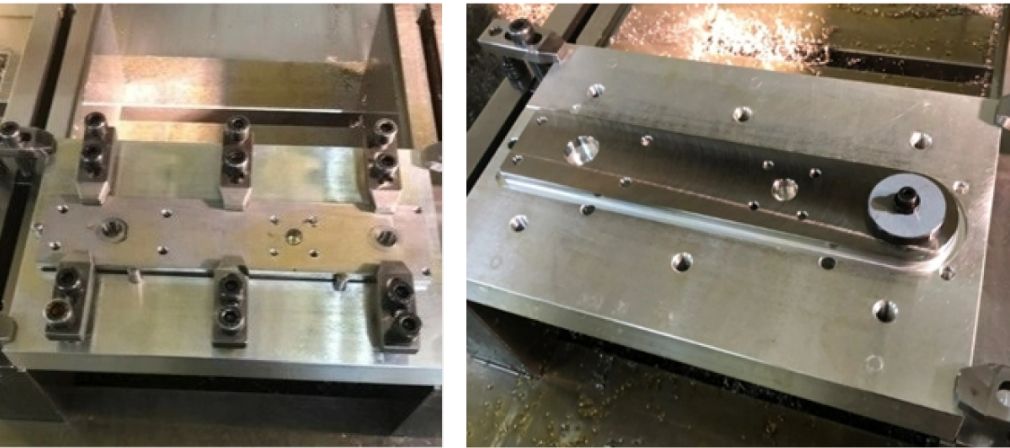
宇宙と時計に、新しい軌跡を。
シチズン時計株式会社は、100周年を迎えた今もなお、常に時計の可能性を考え、開発を続けています。今回のプロジェクトもそのひとつです。その舞台裏には困難を乗り越える努力とスーパーチタニウム™の技術が存在しました。
日々、シチズンを支える技術者たちは“BETTER STARTS NOW”の精神で活動しています。
これからも、シチズンは、民間月面探査プログラム「HAKUTO-R」の支援を続けていきます。
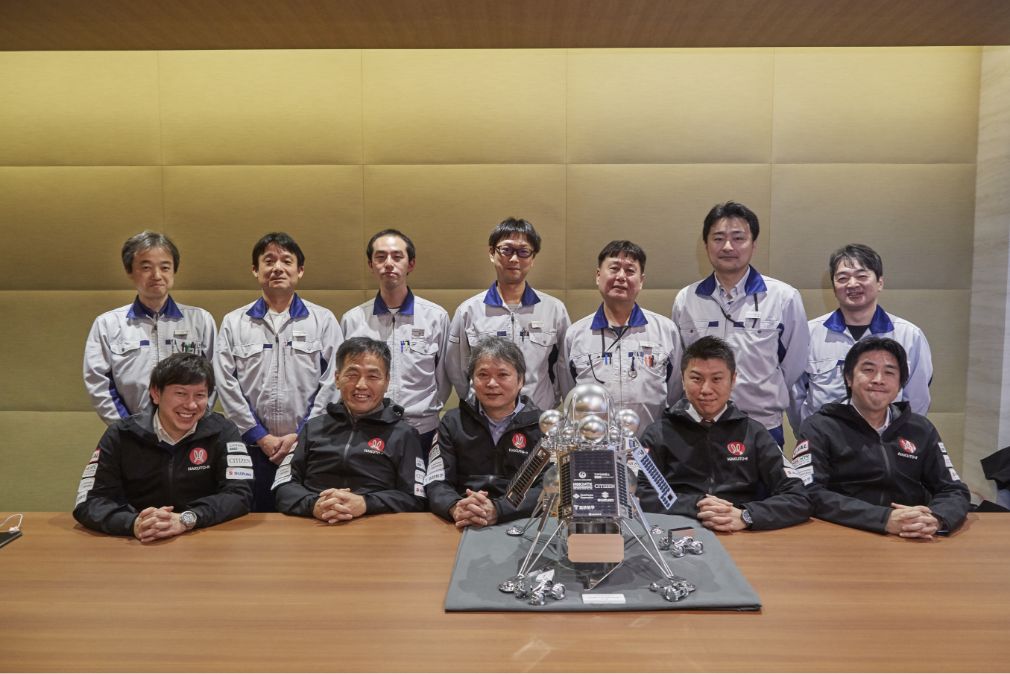
2020年1月撮影
モデル
第5弾特設サイト